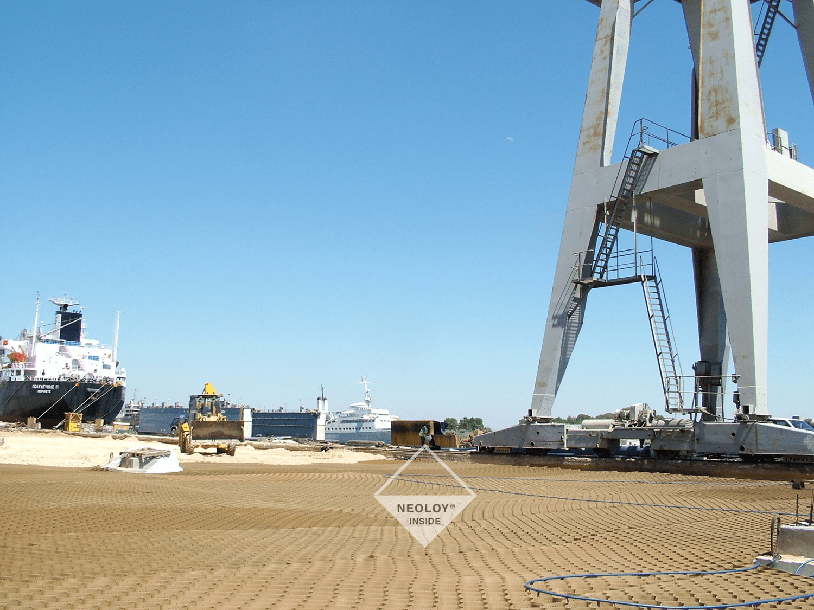
Neoloy Reinforced Pavement for Israel Shipyards
The Tough Cell advanced three-dimensional erosion-control system is the best solution for any slope or channel when erosion is caused by streaming water, including shorelines beach.
Read moreNeoloy Reinforced Pavement for Israel Shipyards
The asphalt pavements of the large working platform docks at the Israel Shipyards suffered severe cracking and deterioration. These are caused by voids in the sand subgrade (which fill the dock’s steel frame) as a result of the saturated marine conditions. Heavy loading from the shipyard’s 400 ton cranes, heavy machinery and container-loaded trucks combined with inadequate structural reinforcement caused failure of the platform surface and substructure layers.
The entire structural pavement needed to be replaced with a solution offering durable reinforcement over the unstable subgrade with sufficient bearing capacity for the entire range of shipyard activities. The shipyard was interested in fast and cost-efficient construction methods to reduce operational downtime and work backlogs.
Conventional Approach
The conventional approach was a 35 cm reinforced concrete pavement structure strong enough to form a bridge over the soft subgrade. This would have required not only large amounts of concrete and steel, but large quantities of high quality aggregate for a 30 cm subbase as well. The estimated construction time and costs involved in such a structure were considerable.
Neoloy Geocell Solution
The Neoloy Geocell confinement system was chosen for the wharf rehabilitation for its engineering advantages (load bearing and distribution, reduced settlement) and long-term design strength. The entire pavement structure was first removed due to excessive damage. Then 20 cm of Neoloy Geocell infilled with local sand was installed over the geotextile and compacted sand subgrade. 100% infill compaction was certified by Nuclear Gauge and GeoGauge devices. Above the Neoloy, a 12 cm granular subbase layer and a well-graded 20 cm aggregate layer stabilized with 5% cement were installed. The surface layer was comprised of 10 cm standard concrete paving blocks on a 3 cm compacted sand leveling course.
Benefits
- Fast installation
- Increased load bearing and distribution meets shipyard’s requirements
- Semi-rigid mattress reduces differential settlement thereby minimizing degradation
- Excellent drainage and durability in saturated conditions best suited for marine platform
- Use of local sand for structural infill
- Long term durable life-span
- Cost-effective
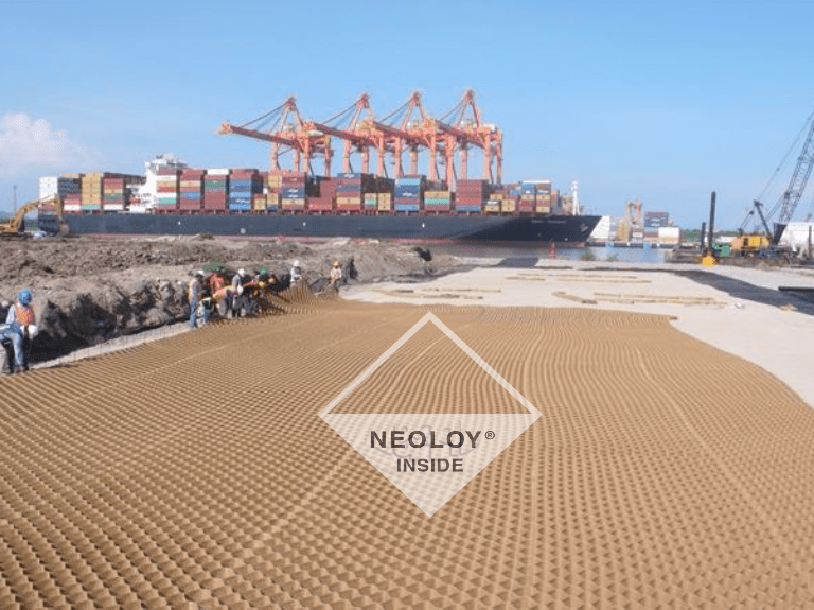
Load Transfer Platforms for Vertical Columns, Mexico
Neoloy® Geocells provided load transfer platform on saturated silty sand, for heavy port platform, Manizillo, Mexico
Read moreLoad Transfer Platforms for Vertical Columns, Mexico
Challenge
A new 150,000 square meter multiple use terminal (MUT) was planned for Manzanillo port to handle 2.5 million tons of general purpose cargo and bulk minerals per year. The contractor was to build five 10,000 sq m platforms within a year with environmental friendly operating equipment and infrastructure. Construction was to be according to the highest international standards with a goal to exceed the planned handling capacity.
The only problem was the extreme site conditions for the terminal platform. The soil was saturated silty sand with a CBR <2%. Bulk handling of lead and zinc minerals, piled into mountains of ore on the dock could reach loads of 35 ton/m2. The terminal foundation was constructed on vertical columns; therefore the reinforcement solution had to function as a load transfer platform as well.
Due to the extreme site conditions and project requirements, Innovator and Ancora Engineering worked together with PRS to develop a reliable design for a geocell reinforced load transfer platform (LTP).
Conventional Solution
Load transfer platforms of concrete, hydraulic-bonded or composite geosynthetic (geogrid) layers were too expensive or insufficient. The thickness of an unreinforced solution would have been much thicker and costly.
Neoloy Geocell Solution
Neoloy Geocells were chosen for their excellent load distribution mechanism. Neoloy reinforcement acts as a stiff mattress, distributing vertical loads widely and reducing settlements. This effectively transfers applied loads directly to vertical columns.
First a 5 cm working platform of lightweight concrete was poured to create a stable working foundation, after subgrade excavation and capping.
Two layers of Neoloy 330-120 (120 mm height) with 12 cm of 1” gravel fill were installed directly over the working platform and compacted with an extra 3 cm overfill over each layer. A layer of 115 cm controlled subgrade undercut was placed with quality controlled compaction every 15 cm. The subgrade layer had a high elastic modulus (178 MPa) due to the Neoloy Geocell reinforcement.
An additional layer of Neoloy Geocell 330-120 was installed in the base layer filled with base quality granular aggregate (+3 cm overfill). The 20 cm base layer also had a very high modulus, as a result of the Neoloy reinforcement. The platform surface layer was 25 cm Portland Concrete Cement slab.
Benefits
- Fast, simple installation – 4 weeks to install 10,000 sq m of pavement
- Modulus Improvement Factor – by 2-3x; enabled use of subgrade material
- Subgrade improvement – 3D “mattress” stabilized extreme subgrade conditions
- Confined drainage system – mission critical considering site conditions
- Cost savings – reduced subgrade extraction, subbase and concrete layers
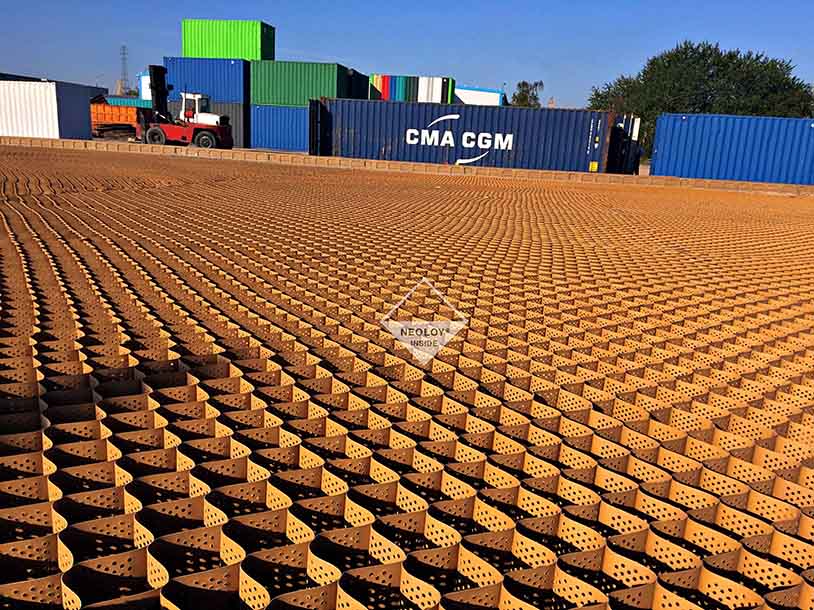
Neoloy® Geocell Reinforced Base for Container Yard, Gdansk, Poland
Neoloy Geocells add tensile stiffness and strength for durable pavements subject to heavy-duty dynamic and static loading.
Read moreNeoloy® Geocell Reinforced Base for Container Yard, Gdansk, Poland
The Challenge
Balticon container terminal operator was expanding storage yard capacity to deal with facility growth at the port of Gdansk. Pavement loading of intermodal container yard operations is extreme – dynamic loading of Reach Stackers lifting containers reaches 1000 kN per axle when lifting containers and stacking 5-high. Strong pavement structural and stable subgrade are required.
The site soil conditions were heterogeneous, saturated sand pocketed with numerous 300m deep holes caused by local gemstone mining operations. Subgrade modulus was 40 MPa. To achieve a basic working layer, the deep holes were first filled with local sand and then dynamic compaction was used to increase soil density.
While geocells were considered for to improve the subgrade strength, only Neoloy Geocells had the required modulus improvement factor – due to their unique engineering performance properties:
- High dynamic (elastic) stiffness (>500 Mpa @ 60°C) – for heavy dynamic loading with low rutting
- High tensile strength (>19 kN/m perforated) – for reliable load distribution under static loading without settlements
- Low permanent deformation (<3% at 75 years) – for long-term performance
Conventional Solution
Chemical stabilizers were deemed insufficient for subgrade stabilization. In addition to high costs, and complicated application, they have limited long-term reliability and may leach into local soil or water-tables.
Neoloy Geocell Solution
Geocell 330 120 category C was chosen for the subgrade/subbase improvement. Neoloy created a stiff homogenous layer over the damaged native soil. Locally dredged sand from port deepening works and hydrotechnical constructions was used for infill.
Although the design goal was 120 MPa, the Neoloy stabilization improved the subgrade modulus by more than 6x from 40 to 250 MPa. The Neoloy Subgrade Improvement Factor (SIF) was verified by static plate testing.
The Neoloy composite system forms a semi-rigid mattress, which acts like a slab. The slab effect reduces vertical pressure and neutralizes differential settlement for reliable container yard pavement performance. The Neoloy subbase also serves as a self-draining system.
Although the original design called for a 30 cm thick C30/37 class rolled concrete base, the high Neoloy SIF enabled a 33% reduction in the concrete layer. The extra 10 cm of concrete was replaced by local sand overfill above the Neoloy layer. The surface course was 10 cm concrete paving blocks over 4 cm cementstabilized sand bed.
Benefits
- Subgrade bearing capacity improved by 6x – while significantly improving the modulus of structural layers above the Neoloy
- Sustainable benefits – reduce site construction and carbon footprints, by using locally dredged sand for infill, instead of imported aggregate
- 30% cost savings – in construction and total life cycle costs
- Simple logistics, rapid installation – 2000 sqm/day
- Improved pavement lifespan – low maintenance